Budowa maszyn pneumatycznych
Budowa maszyn pneumatycznych opiera się na kilku kluczowych elementach, które współdziałają ze sobą, aby zapewnić efektywne działanie systemu. Podstawowym komponentem jest sprężarka, która odpowiada za wytwarzanie sprężonego powietrza. Sprężarka może mieć różne typy, takie jak tłokowe, śrubowe czy wirnikowe, a wybór odpowiedniego modelu zależy od wymagań aplikacji. Kolejnym istotnym elementem są zbiorniki na sprężone powietrze, które gromadzą energię i stabilizują ciśnienie w systemie. Zbiorniki te muszą być odpowiednio zaprojektowane, aby wytrzymać wysokie ciśnienia oraz zapewnić bezpieczeństwo użytkowania. Następnie mamy do czynienia z różnorodnymi zaworami, które kontrolują przepływ powietrza w systemie. Zawory te mogą być ręczne lub automatyczne, a ich właściwy dobór ma kluczowe znaczenie dla efektywności całego układu. Oprócz tego ważne są również siłowniki pneumatyczne, które przekształcają energię sprężonego powietrza w ruch mechaniczny. Siłowniki te występują w różnych formach, takich jak cylindry jednostronnego lub dwustronnego działania, co pozwala na dostosowanie ich do specyficznych potrzeb aplikacji.
Jakie zastosowania mają maszyny pneumatyczne w przemyśle
Maszyny pneumatyczne znajdują szerokie zastosowanie w różnych gałęziach przemysłu, co czyni je niezwykle wszechstronnymi narzędziami. W przemyśle produkcyjnym są one wykorzystywane do automatyzacji procesów montażowych oraz pakowania produktów. Dzięki swojej szybkości i precyzji maszyny pneumatyczne zwiększają wydajność produkcji oraz redukują ryzyko błędów ludzkich. W branży budowlanej maszyny pneumatyczne służą do obsługi narzędzi takich jak młoty pneumatyczne czy wiertnice, co znacznie ułatwia wykonywanie ciężkich prac budowlanych. W sektorze motoryzacyjnym maszyny te są wykorzystywane do lakierowania oraz montażu komponentów samochodowych. Ich zdolność do generowania dużych sił przy jednoczesnym zachowaniu precyzji sprawia, że są idealnym rozwiązaniem w tych zastosowaniach. Dodatkowo maszyny pneumatyczne znajdują zastosowanie w logistyce i magazynowaniu, gdzie używa się ich do podnoszenia i transportowania ciężkich ładunków.
Jakie są zalety i wady maszyn pneumatycznych
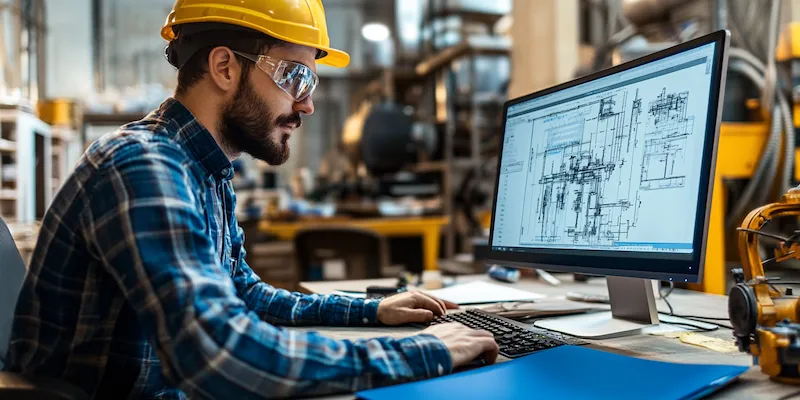
Maszyny pneumatyczne mają wiele zalet, które przyciągają uwagę inżynierów i przedsiębiorców. Jedną z głównych korzyści jest ich prostota konstrukcji oraz łatwość w obsłudze. Systemy pneumatyczne wymagają mniej skomplikowanej infrastruktury niż hydrauliczne czy elektryczne odpowiedniki, co obniża koszty instalacji i konserwacji. Ponadto maszyny te charakteryzują się dużą niezawodnością oraz długowiecznością, co czyni je atrakcyjnym rozwiązaniem dla wielu branż przemysłowych. Sprężone powietrze jest również stosunkowo tanim medium roboczym w porównaniu do innych źródeł energii. Niemniej jednak istnieją także pewne wady związane z używaniem maszyn pneumatycznych. Przede wszystkim efektywność energetyczna systemów pneumatycznych może być niższa niż w przypadku innych technologii, takich jak hydraulika czy elektryka. Straty energii związane z kompresją powietrza mogą prowadzić do wyższych kosztów eksploatacyjnych w dłuższej perspektywie czasowej. Dodatkowo sprężone powietrze może być podatne na zmiany temperatury i wilgotności, co wpływa na jego właściwości robocze oraz jakość pracy maszyn.
Jakie innowacje wpływają na rozwój maszyn pneumatycznych
Rozwój technologii ma ogromny wpływ na budowę maszyn pneumatycznych oraz ich zastosowanie w różnych dziedzinach przemysłu. Innowacje takie jak inteligentne systemy sterowania oraz automatyka przemysłowa umożliwiają bardziej precyzyjne zarządzanie procesami produkcyjnymi z wykorzystaniem maszyn pneumatycznych. Dzięki zastosowaniu czujników i systemów monitorujących możliwe jest zbieranie danych dotyczących wydajności pracy maszyn oraz ich stanu technicznego, co pozwala na szybsze diagnozowanie problemów i optymalizację procesów produkcyjnych. Ponadto rozwój materiałów o wysokiej wytrzymałości oraz lekkich kompozytów przyczynia się do zwiększenia efektywności maszyn pneumatycznych poprzez zmniejszenie ich masy i poprawę wydajności energetycznej. Warto również zwrócić uwagę na rosnące zainteresowanie ekologicznymi rozwiązaniami technologicznymi, które mają na celu ograniczenie zużycia energii oraz emisji CO2 związanej z pracą maszyn pneumatycznych.
Jakie są kluczowe zasady bezpieczeństwa w pracy z maszynami pneumatycznymi
Bezpieczeństwo w pracy z maszynami pneumatycznymi jest niezwykle istotne, zwłaszcza biorąc pod uwagę potencjalne zagrożenia związane z ich użytkowaniem. Przede wszystkim, przed rozpoczęciem pracy z systemem pneumatycznym, należy przeprowadzić dokładną inspekcję wszystkich komponentów, takich jak sprężarki, zbiorniki, zawory i siłowniki. Wszelkie uszkodzenia lub nieprawidłowości powinny być natychmiast zgłaszane i naprawiane, aby uniknąć poważnych awarii. Kolejnym kluczowym aspektem jest stosowanie odpowiednich środków ochrony osobistej, takich jak gogle ochronne, rękawice czy zatyczki do uszu. Użytkownicy powinni być również przeszkoleni w zakresie obsługi maszyn pneumatycznych oraz znajomości procedur awaryjnych. Ważne jest także, aby przestrzegać zasad dotyczących ciśnienia roboczego. Przekroczenie zalecanego ciśnienia może prowadzić do wybuchu zbiornika lub uszkodzenia innych elementów systemu. Należy również pamiętać o regularnym serwisowaniu maszyn oraz wymianie filtrów i osuszaczy, co pozwoli na utrzymanie wysokiej jakości sprężonego powietrza i minimalizację ryzyka awarii.
Jakie są najczęstsze problemy związane z maszynami pneumatycznymi
Maszyny pneumatyczne, mimo swojej niezawodności, mogą napotykać różnorodne problemy w trakcie eksploatacji. Jednym z najczęstszych problemów jest spadek ciśnienia sprężonego powietrza, który może prowadzić do obniżenia wydajności całego systemu. Przyczyną tego zjawiska mogą być nieszczelności w instalacji lub zużyte uszczelki. Warto regularnie kontrolować wszystkie połączenia oraz elementy układu pneumatycznego, aby szybko identyfikować i eliminować źródła nieszczelności. Innym częstym problemem jest kondensacja wody w zbiornikach sprężonego powietrza, co może prowadzić do korozji oraz uszkodzeń elementów maszyny. Dlatego tak ważne jest stosowanie osuszaczy oraz regularne opróżnianie zbiorników z nadmiaru skroplin. Ponadto użytkownicy mogą napotykać trudności związane z działaniem zaworów, które mogą się zaciąć lub nie działać poprawnie z powodu nagromadzenia brudu czy kurzu. Regularne czyszczenie i konserwacja zaworów są kluczowe dla zapewnienia ich prawidłowego funkcjonowania.
Jakie są różnice między maszynami pneumatycznymi a hydraulicznymi
Maszyny pneumatyczne i hydrauliczne to dwa różne typy systemów mechanicznych, które mają swoje unikalne cechy oraz zastosowania. Główna różnica między nimi polega na medium roboczym: maszyny pneumatyczne wykorzystują sprężone powietrze, podczas gdy maszyny hydrauliczne operują cieczą pod ciśnieniem. Dzięki temu maszyny pneumatyczne są zazwyczaj lżejsze i prostsze w budowie niż ich hydrauliczne odpowiedniki. Pneumatyka charakteryzuje się również szybszym czasem reakcji oraz mniejszymi wymaganiami dotyczącymi konserwacji. Z drugiej strony maszyny hydrauliczne oferują znacznie większą siłę działania przy mniejszych rozmiarach jednostek wykonawczych, co czyni je bardziej odpowiednimi do zastosowań wymagających dużych obciążeń i precyzyjnego sterowania ruchem. Dodatkowo hydraulika ma lepszą efektywność energetyczną w porównaniu do pneumatyki, zwłaszcza w dłuższej perspektywie czasowej. Warto również zauważyć, że maszyny hydrauliczne mogą działać w trudniejszych warunkach atmosferycznych oraz przy wyższych temperaturach niż systemy pneumatyczne.
Jakie są przyszłościowe kierunki rozwoju technologii pneumatycznej
Przyszłość technologii pneumatycznej rysuje się w jasnych barwach dzięki ciągłemu postępowi technologicznemu oraz rosnącemu zainteresowaniu automatyzacją procesów przemysłowych. Jednym z kluczowych kierunków rozwoju jest integracja systemów pneumatycznych z nowoczesnymi rozwiązaniami cyfrowymi oraz Internetem Rzeczy (IoT). Dzięki temu możliwe będzie monitorowanie stanu maszyn w czasie rzeczywistym oraz optymalizacja ich pracy na podstawie danych analitycznych. Tego rodzaju innowacje pozwolą na zwiększenie efektywności produkcji oraz redukcję kosztów eksploatacyjnych poprzez lepsze zarządzanie zasobami energetycznymi i materiałowymi. Kolejnym istotnym trendem jest rozwój ekologicznych rozwiązań technologicznych, które mają na celu zmniejszenie zużycia energii oraz emisji CO2 związanej z pracą maszyn pneumatycznych. Wprowadzenie bardziej efektywnych systemów kompresji powietrza oraz recyklingu sprężonego powietrza staje się priorytetem dla wielu producentów sprzętu pneumatycznego. Dodatkowo rośnie zainteresowanie zastosowaniem materiałów kompozytowych o wysokiej wytrzymałości w konstrukcji elementów maszyn pneumatycznych, co pozwoli na dalsze zwiększenie ich wydajności oraz trwałości.
Jakie są koszty eksploatacji maszyn pneumatycznych
Koszty eksploatacji maszyn pneumatycznych mogą być różnorodne i zależą od wielu czynników, takich jak rodzaj zastosowania, intensywność pracy czy jakość używanego sprzętu. Jednym z głównych składników kosztów eksploatacyjnych jest energia potrzebna do działania sprężarek powietrza. Koszt energii elektrycznej może znacząco wpłynąć na całkowite wydatki związane z użytkowaniem systemu pneumatycznego. Dlatego tak ważne jest wybieranie energooszczędnych modeli sprężarek oraz optymalizacja procesów produkcyjnych w celu minimalizacji zużycia energii. Kolejnym istotnym czynnikiem wpływającym na koszty eksploatacji są wydatki związane z konserwacją i serwisowaniem urządzeń. Regularne przeglądy techniczne oraz wymiana filtrów czy uszczelek są niezbędne dla zapewnienia prawidłowego funkcjonowania systemu i uniknięcia kosztownych awarii. Dodatkowo warto uwzględnić koszty zakupu części zamiennych oraz ewentualnych napraw urządzeń w przypadku wystąpienia usterek.